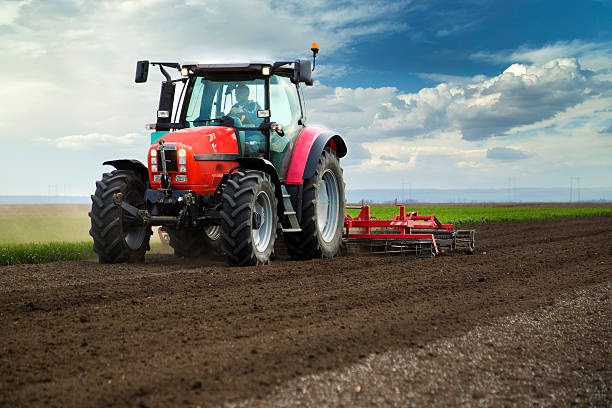
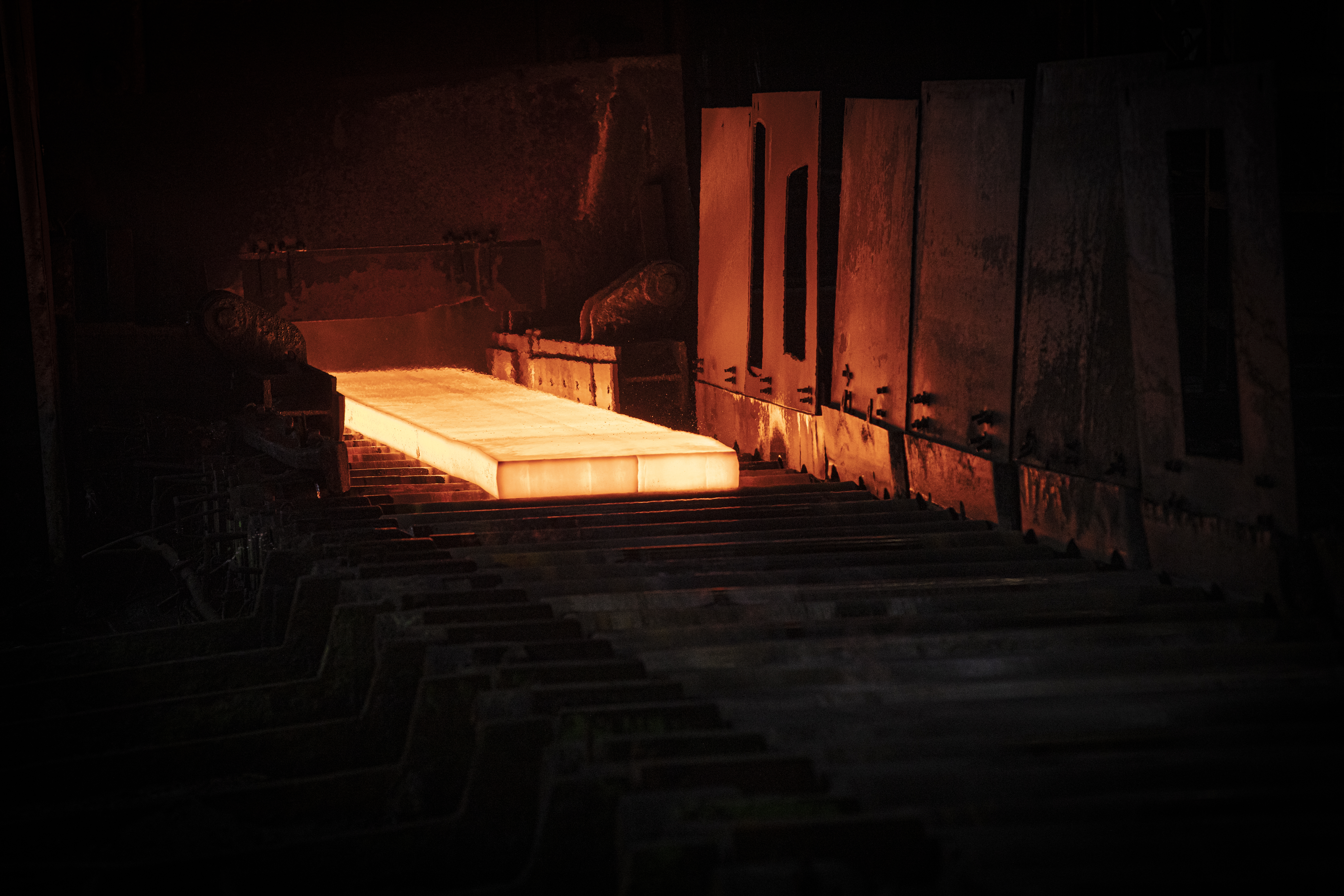
New technologies and advancements in hot-rolled coil manufacturing
In the steel industry, continuous innovation is the key to sustaining growth and efficiency. Hot rolled steel remains a cornerstone in various industrial applications, from construction to automotive manufacturing. This blog explores the latest advancements in AM/NS India’s hot rolled coil manufacturing, shedding light on cutting-edge technologies that are reshaping the steel production landscape.
State-of-the-Art Hot-Rolled Coil Manufacturing Technologies
High-Performance Furnaces
The heart of any steel manufacturing plant is its furnace, and recent advancements have transformed these crucial components into high-performance marvels. Modern furnaces boast enhanced energy efficiency, resulting in a more sustainable and cost-effective hot rolled steel production process. This improvement not only reduces operational costs but also aligns with global sustainability goals.
Advanced Rolling Mills
The backbone of hot rolled coil manufacturing, rolling mills have witnessed significant technological upgrades. High-speed and precision-controlled rolling mills ensure uniform thickness and superior surface quality of the steel coils. These advancements translate into improved product performance and increased customer satisfaction.
Artificial Intelligence and Automation
In an era dominated by Industry 4.0, artificial intelligence (AI) and automation have penetrated every aspect of manufacturing, and hot rolled steel production is no exception. Smart manufacturing processes driven by AI algorithms optimize production parameters, leading to higher productivity and reduced downtime. Automation not only improves efficiency but also ensures a safer working environment by minimizing manual intervention in high-risk areas.
DRI Manufacturing Method: A Game-Changer in Steel Production
One notable development in AM/NS India’s hot rolled coil manufacturing is the Direct Reduced Iron (DRI) manufacturing method. DRI serves as a high-quality alternative to traditional iron ore in the steelmaking process. This method involves the reduction of iron ore using natural gas or hydrogen, producing a highly pure and consistent iron feedstock.
DRI offers several advantages in hot rolled steel production, including reduced greenhouse gas emissions, lower energy consumption, and increased operational flexibility. This innovative approach has gained prominence in the industry due to its environmental sustainability and potential cost savings. Several steel plants in India have successfully implemented the DRI manufacturing method, positioning the country as a hub for sustainable steel production.
The DRI method involves a two-step process: first, the reduction of iron ore to DRI pellets, and second, the use of these pellets in electric arc furnaces for steelmaking. The reduction process significantly lowers carbon dioxide emissions compared to traditional methods, contributing to a greener and more sustainable steel industry.
Hot Rolled Steel in India: A Growing Industry
India has emerged as a significant player in the global steel market, with numerous steel manufacturing plants adopting the latest technologies for hot rolled coil production. AM/NS steel plant in India is characterized by its scale, efficiency, and commitment to sustainable practices. As the demand for high-quality steel continues to rise, Indian steel manufacturers are leveraging advanced technologies to meet these requirements while minimizing environmental impact.
Facts and Figures
- According to recent industry reports, the global hot rolled steel market is projected to reach a value of USD 102.89 billion by 2027, with a compound annual growth rate (CAGR) of 6.7% from 2020 to 2027.
- India's steel production reached approximately 111.2 million metric tons in the fiscal year 2020-21, making it the second-largest steel-producing country globally.
- The implementation of DRI technology at the steel plant in India has contributed to a 20% reduction in carbon emissions compared to traditional steelmaking methods.
Conclusion
The landscape of hot rolled coil manufacturing is undergoing a significant transformation with the integration of cutting-edge technologies and the adoption of sustainable practices. High-performance furnaces, advanced rolling mills, and the revolutionary DRI manufacturing method are driving the industry towards increased efficiency, reduced environmental impact, and superior product quality.
As India continues to play a pivotal role in the global steel market, steel plants in the country are at the forefront of embracing these innovations. AM/NS India’s steel manufacturing plant in India is evolving into a hub of technological excellence, contributing not only to economic growth but also to a more sustainable and environmentally conscious future for the steel industry. With continuous advancements, the hot rolled steel sector is poised for further growth and excellence in the years to come, meeting the demands of industry experts and developers worldwide.
Explore our latest Post
- Market Dynamics: Analyzing The Demand And Supply Of Hot Rolled Steel In India
- Hot Rolled Steel Sheets And Coils: Versatile Industrial Materials
- The Role Of AM/NS Stallion In Improving Modern-Day Agriculture
- The Manufacturing Process Behind Hot Rolled Steel
- Hot Rolled vs Cold Rolled Steel: Understanding the Differences
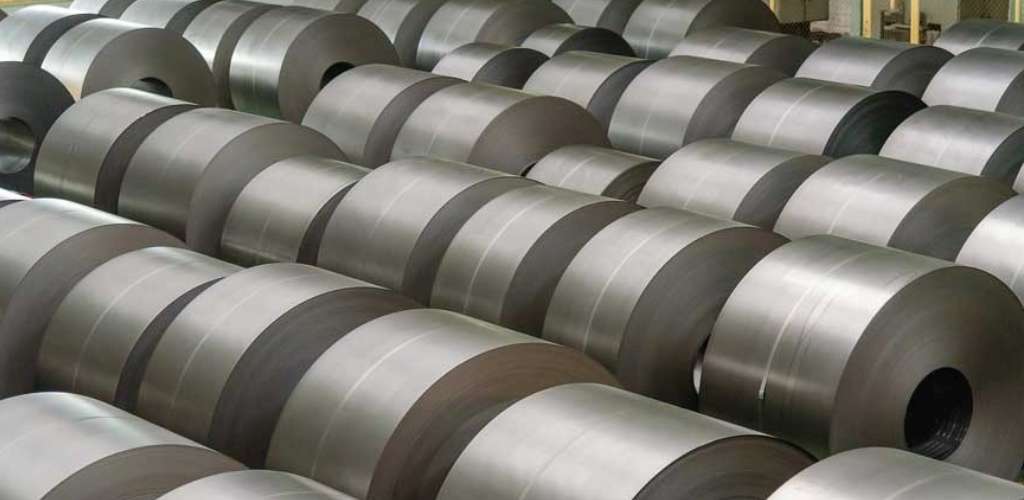